Mechanical Technician
San Fernando, South West
Full time
Posted On 04.29.2025
Expire On 05.07.2025 Employer
Description
JOB PURPOSE
The primary purpose of the Mechanical Technician is to ensure the efficient operation, maintenance, and repair of mechanical systems and equipment within an industrial setting. Apart from the aforementioned, he/she will ensure that all products and services meet the highest quality standards throughout the execution, production and service delivery processes.
This role involves diagnosing mechanical issues, performing inspections, and executing maintenance ensuring quality and safety compliance with industry standards and regulations.
This position requires strong technical skills, an in-depth understanding of mechanical systems, ability to perform quality checks and verifications, Preparation of detailed reports on quality performance, inspection findings, non-conformities, and action plans. And the ability to work in fast-paced, high-demand environments.
DUTIES AND RESPONSIBILITIES
Primary Responsibilities
- Rotating Equipment Expertise: Take full responsibility for all aspects of rotating equipment repairs in the workshop, including disassembly, inspection, refurbishment, reassembly, and testing. Ensure adherence to internal processes, applicable industry standards (e.g., API), and OEM specifications.
- Collaborative Troubleshooting & Problem-Solving: Work in close coordination with other technical teams to identify, troubleshoot, and resolve mechanical issues. Implement effective solutions to ensure machinery and systems are operating at optimal levels, minimizing downtime, and enhancing overall organizational efficiency.
- Equipment Dismantling, Inspection, and Measurement: Dismantle and thoroughly inspect mechanical equipment, ensuring accurate measurements and identification of potential issues or areas for improvement.
- Assembly of Equipment: Assemble rotating and static equipment, ensuring proper alignment, installation, and functionality. Verify that all components are working as intended, and make adjustments as necessary. Performance of dimensional and fitment checks using precision instruments ensuring we meet OEM, specification and Industry standards.
- Quality Assurance & Compliance: Promote where necessary and adhere to the company’s Quality Assurance (QA) and Quality Control (QC) policies and procedures, ensuring high standards of mechanical work and service. Maintain full compliance with industry standards and relevant regulations.
- Testing and Calibration of Equipment: Apply advanced balancing and alignment techniques, to mechanical equipment, ensuring we achieve optimal function, specification and performance per OEM ISO standards.
- Interpret readings from tests and measurements, determining whether further corrective actions are required.
- NDT Testing- Ability to perform NDT (dye pen) testing to equipment and interpret results
- Data Interpretation & Technical Reporting: Analyze test results and data readings from verification tests to assess the condition and performance of mechanical systems. Compile technical reports with actionable recommendations based on these findings.
- Detailed Reporting & Recommendations: Compile and present comprehensive reports that include technical findings, assessments, and actionable recommendations to improve equipment performance and prevent future breakdowns.
- Housekeeping & Workplace Organization: Ensure consistent and thorough housekeeping practices are followed within the workshop and work areas, maintaining a clean, safe, and organized environment for optimal productivity.
Other Responsibilities
- Job Safety & Compliance Documentation: Complete Job Safety Analysis (JSA) forms, ensuring all safety protocols are adhered to during operations. Fill out job scopes accurately to provide clarity on tasks and safety considerations.
- Excellent Computer Literacy – Ability to use computer/tablet for maneuvering necessary Apps and software for generating reports and inspection findings.
- Representation of Company Standards: Serve as a positive and professional representative of the company, upholding organizational values and fostering strong relationships with colleagues, clients, and external stakeholders.
- Cross-Functional Team Collaboration: Work harmoniously with internal teams and external partners to address client needs, optimize business performance, and achieve corporate goals.
- Adherence to External Standards: Integrate external standards and best practices into internal systems, ensuring that all processes, tools, and equipment meet or exceed industry benchmarks. Maintain alignment with relevant regulatory bodies and incorporate their guidelines into daily operations.
Quality and HSE Responsibilities
- Assist in the completion of Job Safety Analyses (JSAs), inspection forms, and checklists for both organizational and site activities.
- Identify and address workplace safety hazards, ensuring that all coworkers are informed and aware of potential risks.
- Contribute to HSE improvement proposals by clearly outlining non-conformance issues, proposing corrective actions, and defining the resources and implementation plans required.
- Support the implementation of Job Safety Analyses (JSAs) and actively monitor job site activities, particularly in high-risk or hazardous situations.
- Participate in accident and near-miss investigations, contributing to root cause analysis and corrective action recommendations.
- Review and analyze accident and near-miss incidents when required, providing actionable recommendations for safety improvements.
- Read, understand, and comply with the company's HSE policies, work practices, procedures, and safety rules.
- Properly wear and maintain all personal protective equipment (PPE) as required by the company’s HSE policy.
- Utilize and maintain all required safety equipment in accordance with company HSE guidelines.
- Report all accidents and incidents promptly to the supervisor and follow the procedures outlined in the Accident/Incident Reporting Policy.
- Immediately inform the supervisor of any unsafe acts, conditions, or potential hazards in the workplace.
- Take all reasonable precautions to protect personal health, safety, and the environment while performing work tasks.
- Attend all environment, health, and safety meetings as specified in the HSE policy.
- Fully cooperate with management and colleagues to ensure the fulfillment of all HSE obligations.
- Recognize the right to halt any work deemed unsafe, ensuring the safety of all personnel.
- Adhere to and assist in the implementation of all relevant health and safety legislation, codes of practice, and company safety procedures.
- Avoid actions that present a danger to oneself or others, ensuring a safe working environment.
- Avoid improvising work practices that may introduce unnecessary risks.
- Alert new employees to known hazards and risks within the workplace.
- Refrain from engaging in horseplay or misusing welfare facilities.
- Actively suggest improvements or methods for eliminating identified hazards.
- Only operate machinery or equipment after receiving proper training and authorization.
Context
- OPERATING ENVIRONMENT: This position is required in the Mechanical Workshop and on-site as and when required.
- FRAMEWORK AND BOUNDARIES: The Mechanical Technician will be guided by the policies and procedures of the Company. Directions are provided as an when required, pertaining to non-routine issues that need input and advice of the Project Engineer, Operations Manager and Managing Director.
Job Requirements and Specification:
Education Skills and Training
- High school diploma or CXC passes.
- MET diploma or equivalent qualifications from a certified institute.
Core Competencies
- Knowledge of Mathematics pertaining to machinery.
- Knowledge of machines and tools.
- Quality checking
- Analytical and problem-solving skills.
- Written and verbal communication skills.
- Computer Literacy.
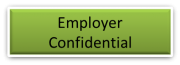
Employer Confidential
View Company Profile
View Saved Jobs Tell a Friend Print This Ad Report This Job
Overview
Tags
Job Requirements
- High school diploma or CXC passes.
- MET diploma or equivalent qualifications from a certified institute.
Core Competencies
- Knowledge of Mathematics pertaining to machinery.
- Knowledge of machines and tools.
- Quality checking
- Analytical and problem-solving skills.
- Written and verbal communication skills.
- Computer Literacy.
Career Advice
BROWSE JOBSBoost Your Job Prospects: How to Earn Additional CXC/CSEC Passes in Trinidad and Tobago
Discover Top Institutions and Programs to Enhance Your Qualifications and Land Your Dream Job Are you struggling to land an entry-level job in Trinidad and Tobago with three or fewer CXC CSEC passes …
Read More